I went to a school auction yesterday and scored a Southbend metal lathe. I haven't had time to mess with it yet, or even research it, but it is a good size for my garage shop and what I've read on-line suggests that the old Southbend lathes are a good bet with parts generally available and heavy construction that lends to long life. Having been in a school, I'm sure it has been abused; the rails look pretty dinged up. But since I'm not going to be trying to make anything with close tolerance, it should be good for general purpose.
Obviously, it has a 3 phase motor. But since I am already using a variable frequency drive on my 3 phase vertical mill, I'm thinking I will be able to run the lathe off the same drive and not have to buy another one. I just wont be able to run them simultaneously. I'll probably wire in a disconnect so that its not possible to accidently have them both in the "on" position at the same time.
Moving this dude presented the same problems as with the Mill; it is one heavy SOB. They loved iron back then. I could budge the tail stock end manually, but not the gear end. Also, I had to get it out by 5PM. By the time I got back to my office to get a stakebed and some tools, and back to the school (30 min. drive each way) it was 4PM. The guys in charge were school system employees, so you can bet there was no assistance available and they would be locking the doors at 4:50.
At home, I quickly removed my machine mover from the mill in my shop. This involved putting it up on temporary blocks. Sounds easy? Not. I had to plane some oak cribbing to the exact thickness of the gap between the rails of the mover and the slab, then wedge them in and unbolt the mover and pull out the rails (see earlier post for pictures). I grabbed some wood cribbing and a spud bar, and was off to the school. The lift gate on my stakebed--a gift from God himself--is good for 1,750 lbs. It barely worked for the mill, but the lathe looked to be a lot less heavy.
Back at the school with the clock running, I worked frantically and got my wheel rails lined up and the cross rails in place to bolt together under the lathe once I got it up on blocks. The details of this effort are hard to describe. I used the spud bar as a lever and the wood cribbing for both a fulcrum and to block the corners up a little at a time, being careful to not interfere with placement of the rails which would have to slide in around the base. Suffice to say that I was able to get this thing out the door as they were turning the key in the locks behind me. Fortunately it was a beautiful day and breezy, so my sweat drenched clothes dried out a bit on the drive home. I sat down to dinner at 6:30 with the family, the lathe in my garage and the stakebed parked back at the office.
I work alone quite a bit, and one learns tricks and techniques along the way. Most importantly, never forget your good friend Archi Medes. Good old Archi will lift you up and only let you down easy.
“A human being should be able to change a diaper, plan an invasion, butcher a hog, conn a ship, design a building, write a sonnet, balance accounts, build a wall, set a bone, comfort the dying, take orders, give orders, cooperate, act alone, solve equations, analyze a new problem, pitch manure, program a computer, cook a tasty meal, fight efficiently, die gallantly. Specialization is for insects." Robert Anson Heinlein
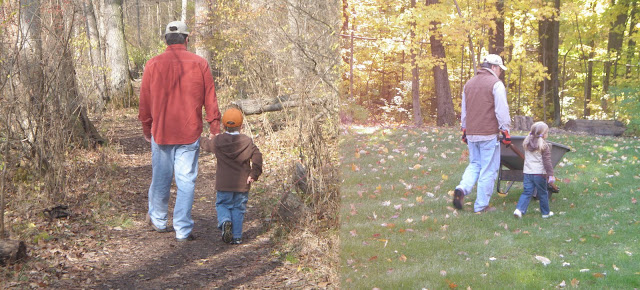
Thursday, April 29, 2010
Monday, April 26, 2010
Yoda
I finally got around to taking a closer look at the Alvarez guitar my friend gave me to take a "crack" at repairing. Several weeks ago, I began to disassemble what was left to disassemble. I took off the strings, which were the only thing holding the neck and body together. I tried to compare the low E to a piece of field fence I dug up out of the back yard, but without a microscope I couldn't make any claims for certain. The neck was broken off the body through the heel, so I planned to remove the rest of the heel from the dovetail and glue it back together. I stripped the hardware off the neck to clean it up. I used mineral spirits to try to get years of grime off the fretboard--this thing has been sitting in a garage for a long time. I ended up taking a chisel to the fretboard to scrape across the grain against each fret. This was not a great idea and yielded poor results.
So this weekend, I decided I would re-fret the thing, since the top three frets were badly grooved. The fret board itself is also worn in the top three frets--from long fingernails I guess. So I removed all of the frets and sanded the entire neck to original wood--it looks much better already. I removed the fake wood headstock cover--it was very disappointing--actual paper printed with fake wood grain and the logo--no inlay at all. I'll make a new real wood cover. I removed the plastic binding and the plastic nut so I can profile the neck properly. I thought about sanding the grooves out, but that would take too much material off. I could just replace the fretboard at this point, but I think I want to keep as much of the original parts as possible; and, not tie too much money into this thing. I will fill the divots with epoxy filler, which should blend well enough. I plan to replace the nut with bone, just for fun. I'll make it from a piece of cow bone--I think I may have a chew toy laying around somewhere from my dear old departed canine. It should machine like wood.
I removed the neck heel from the dovetail by heating it with a heat gun and using a bar clamp to "press" it out of the joint. This was a bit tenuous as it involved a lot of heat and pressure, both of which threatened to reduce the parts of this instrument to ash and splinters. Ultimately, it popped out nicely and I learned that removing a dovetail neck is not too big a deal. I glued the heel back together with the neck and I expect the neck will go back together with the body with minimal trouble.
Now for the major damage. The cracked back looked like I may be able to press the crack back together and glue it up. I made a clamping block and got most of the crack to fit back together, but I just wasn't satisfied that this was going to be adequate. I decided to replace the entire back. It came apart with a fair amount of effort and patience. Unbelievably, of all the tooling at my disposal, a cheap pocket knife worked the best. Although the binding will have to be replaced as well, as it melted from the heat gun and was severely damage by the pocket knife, the sides are very serviceable and I expect no trouble mating a new back and re-binding. I would like to make new wood binding, but since I am not re-binding the entire guitar, I will have to match the existing white plastic on the front. There is real danger of making a silk purse from a sow's ear.
So now I have the thing disassembled and ready for new parts and re-finishing and re-assembly. This week I will acquire the new fret wire and decide if I'm going to buy blanks for the back or make the back from lumber I have laying around. I am trying to keep the front completely untouched. It is the essence of "character" and if it were mine, I would want it untouched. I will clean it up a little, because I simply can't stand the grime. The pickup should be easy to fix--it just needs to be cleaned and re-soldered to a new PL55 jack.
I'm looking forward to finishing this thing. I'm particularly interested in seeing how the glue holds up on the neck.


Now for the major damage. The cracked back looked like I may be able to press the crack back together and glue it up. I made a clamping block and got most of the crack to fit back together, but I just wasn't satisfied that this was going to be adequate. I decided to replace the entire back. It came apart with a fair amount of effort and patience. Unbelievably, of all the tooling at my disposal, a cheap pocket knife worked the best. Although the binding will have to be replaced as well, as it melted from the heat gun and was severely damage by the pocket knife, the sides are very serviceable and I expect no trouble mating a new back and re-binding. I would like to make new wood binding, but since I am not re-binding the entire guitar, I will have to match the existing white plastic on the front. There is real danger of making a silk purse from a sow's ear.
So now I have the thing disassembled and ready for new parts and re-finishing and re-assembly. This week I will acquire the new fret wire and decide if I'm going to buy blanks for the back or make the back from lumber I have laying around. I am trying to keep the front completely untouched. It is the essence of "character" and if it were mine, I would want it untouched. I will clean it up a little, because I simply can't stand the grime. The pickup should be easy to fix--it just needs to be cleaned and re-soldered to a new PL55 jack.
I'm looking forward to finishing this thing. I'm particularly interested in seeing how the glue holds up on the neck.
Subscribe to:
Posts (Atom)